For the carbon fiber industry, 2016 is a brilliant year for achievements. In addition to achieving the production of T800 kilotons of carbon fiber, carbon fiber composite materials have also made some achievements in various fields such as aviation, transportation, industry and civil use Surprising new progress.
Aerospace: The largest carbon fiber solid rocket motor housing
On September 22, 2016, the successful ground test of the first-class solid-propellant rocket engine, developed by nine of the fourth institutes of the China Aerospace Science and Industry Corporation, was successfully completed. It has become the largest size and largest amount of powder coated carbon fiber composite shell technology in China, Solid rocket engine. The engine diameter 2.2m, total length 9.7m, charge 45t, with high quality ratio, high specific impulse, high thrust and so on. The test confirmed the key technologies such as large-size carbon fiber composite shell, high-flow nozzle and large-tonnage charge to realize the leapfrog promotion of large-size carbon fiber composite shell engine engineering application.
Navigation: The first carbon fiber reinforced sandwich structure hull push watertight cover
Shanghai Hu Zhou Industrial Co., Ltd. independently developed a carbon fiber 艏 side push watertight cover, the technology access to China's utility model patents, is currently the first in the international community. Cover body with multi-axis carbon fiber and reinforced resin composite materials, with high strength, light weight, anti-seawater corrosion and other characteristics of the DNVGL test center passed the strength test and obtained DNVGL strength certificate. In addition, the product is a honeycomb sandwich structure, the proportion of side watertight cover is 1, the entire watertight cover can be suspended in water, to facilitate divers underwater operation. To ensure that the watertight cover and the hull linear match, the scene using 3D scanning and computer modeling, calculated by finite element method cover strength, design a reasonable structure, weighing only one-fifth of the weight of the same type of cover abroad , And the intensity to meet the underwater 15 meters to 25 meters operating requirements. The product is mainly for shipping companies in the case of not docked on the side of the ship to promote line maintenance and repair, which greatly saves the cost of docking repair and voyage maintenance time.
High-speed Rail: Flame-retardant carbon fiber composite structure to achieve mass production
Wuxi VIA New Material Technology Co., Ltd. developed a new type of carbon fiber composite with flame retardant, fire retardant, toughening and other properties, the carbon fiber composite materials made of high-speed rail structure has entered the high-volume production stage. In many accidents of aviation, automobile and rail transportation, the accidental collision easily causes the car body to burn. The smoke and harmful substances formed after burning the car body material often result in the increase of the lethality rate, and the new type of carbon fiber composite material can achieve EU EN45545 rail vehicle fire test standards, in case of spontaneous combustion after the fire, the amount of smoke is minimal, does not release harmful gases, can effectively reduce the hazards of accidents on the human body. Moreover, the average speed of China's high-speed railways exceeds 200km / h and the maximum speed reaches 350km / h or above. The ultra-high speed has strict requirements on the structure of the vehicle body and the material of the carriage body. All physical properties of the material must meet the higher standards. Carbon fiber composite parts made of very light quality, but its strength is larger than steel, with its replacement of metal materials, can greatly reduce the weight of the body, while reducing body energy consumption while running, but also enhance the body Security.
Wind power: the first 68 meters long carbon fiber fan blades
From Lianyungang in Jiangsu Lianzhong Composite Materials Group Co., Ltd. independent research and development, the first 68 meters long 6 MW wind turbine blades shipped to Europe recently. It is reported that the blade innovative use of carbon fiber beam vacuum infusion process to overcome the domestic production of large-scale 12K carbon fiber carbon fiber fabric problems, the blade can be widely used in coastal wind farms for the offshore wind turbines in China to lay the foundation for the domestic carbon fiber The application of high-power carbon fiber blade manufacturing to solve the international problems, help to increase our high ground to seize the global wind power industry.
Infrastructure: The successful development of insulated carbon fiber composite core wire
In 2016, September 22, Hohhot Power Supply Bureau Wonshan line line reconstruction project in Hohhot Jinchuan Development Zone cable construction. This line adopts Inner Mongolia Haoyuan New Material Co., Ltd. newly designed and manufactured JKLRXYJQ / F1A-10170/20 insulated carbon fiber composite core wire. This type of wire can be widely used in 10kV and below distribution network capacity expansion transformation and infrastructure lines. It is reported that this new type of wire is still the first application in Inner Mongolia, the carbon fiber composite core wire with light weight, high strength, corrosion resistance, high temperature, large carrying capacity, sag, cost advantages, the annual production capacity 20,000 kilometers, the product is now widely used in power lines of different voltage levels of new lines and old network renovation project.
Civil: the world's first carbon fiber smart robot electric car
Recently, the world's first carbon fiber intelligent robot electric car, by the Eagle Eagle Carbon Bicycle Co., Ltd. independent research and development success, and the public to meet. The carbon fiber smart robot electric car frame with all-carbon fiber materials and advanced molding process, free to shrink and stretch, all-inclusive battery weighs only 15 kg, lightweight body, easy to carry, up to 20 km / h, the largest Load 150 kg, 4 hours charging life can be 30 kilometers, with spare batteries up to 60 km. Automatic folding design concept makes the body easier to fold and more compact, easy to carry, whether it is by bus, subway, or into the elevator, even with the shopping mall are not a problem.
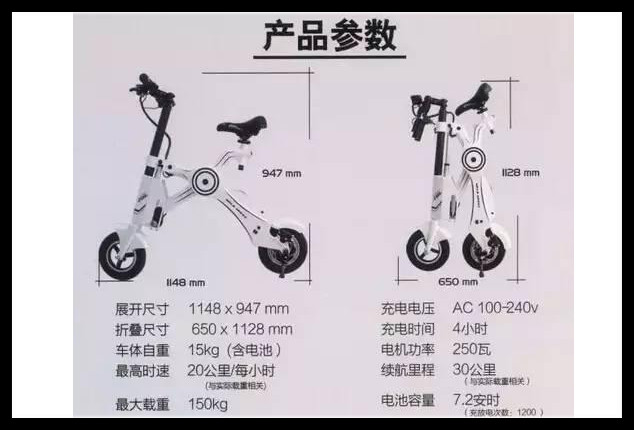